車枠(フレーム)の改造は陸運支局への届けが必要です。
まず、能力強度等検討書の提示により車枠強度を検討します。
通常、各部の変更箇所の面積・材質などの計算式で応力から破壊安全率を出し、書面で認めてもらう方法が最も早い方法です。
しかし、当初の検査課の担当の回答ではまだオートバイの車枠改造(フレーム加工)での公認の実例が無いとのことで、計算式での書面では認められず、実際に車枠の歪量を測定し破壊安全率を出して、それにより検討すると北海道自動車検査独立行政法人担当の回答でした
そこで当社では実際に測定するのが安全性には間違いない事であり、レコーダーを車体に付け計測し歪量を実測しています。
これにより規定安全率をクリアーすれば車枠(フレーム)加工をしても、公認車輌に出来ます。
フレーム加工による公認車輌制作過程をこれから簡単に紹介します
今回紹介するヘベース車輌は1992年ソフテールカスタム FXSTC
国内登録済みの車輌を車枠改造する前にやる事
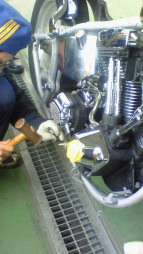
ハーレーの場合、フレームネック部分にシリアル(車体番号)が打ってあります。フレーム加工のためには、この部分を切り離す必要があるため、支局に届けてシリアルを別の場所に移動します。
この際、職権打刻になり、元の打刻は使えませんので、車体番号は変更となります。フレームの加工は違法ではありませんが、勝手に車体番号を切り離すことは違法になります。
車検証のフレーム番号は職権番号になりますが、車名は変わりません。改造検査後、形式に「改」が入ります。
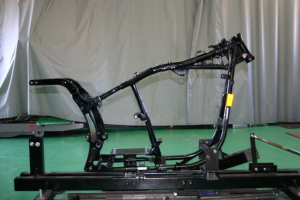
改造箇所は、メインチューブならびにダウンチューブの延長、ネック角パイプを変更し、ロングフロントフォークを装着します。
車体フレームを正確に加工するために、フレームジグに装着して各部水平レベルを出してセットアップし、エンジン・ミッションマウントをしっかりと固定し、作業に取り掛かります。
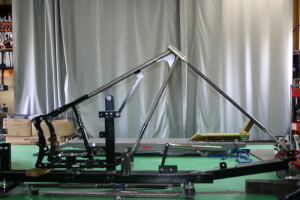
今回はドラゴンスプリンガー20インチオーバーを装着するため、フロントフォークの長さ21インチのタイヤの半径を測り車高を計算して、メインチューブの長さならびにネックパイプの角度を決めます。
既存フレームにパイプ゚径を合わし、ツナギ部分はアダプターを制作し差込で溶接します。ネック部分は補強プレートを制作し溶接して強度を確保します。
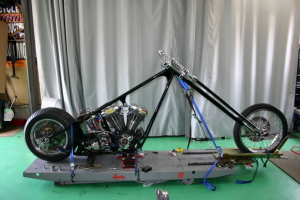
溶接部をきれいに仕上げ、塗装して、フロントフォーク・エンジン・ミッション・タイヤ各部組付け、テスト出来るように車輌を組み上げます。
その際 実際の車輌総重量より少しでも重くするため、ウェイトをつけるなど工夫して組付けます。重い状況で測定をしておくと、実際に公道で走る時は測定した時より軽いので、リスクを軽減するためでもあります。
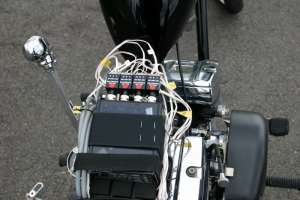
データ解析時に分かりやすいよう、番号を付けた歪ゲージを数十か所に貼り付け、レコーダーを操作しやすい場所にセットします。数種類ある歪ゲージは角用途に合ったものを使用します。
準備が終われば、レコーダーにメモリースロットカードをセットしてスタートします。。
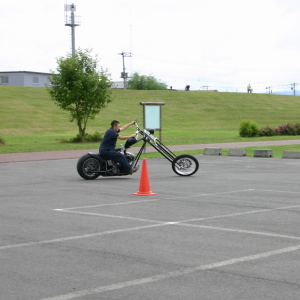
実際の行動を走行するにあたり、様々な条件を予測し、測定をします。
レコーダーが4チャンネルしかないので、1度に4か所しか測定できないため、ゲージの配線を入れ替えながら数十回測定します。
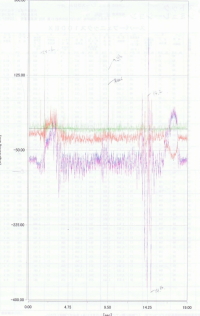
測定終了後はメモリーからデータをパソコンに取り込み、専用ソフトで歪量を解析します。
その際、データはグラフ並びに数値で表示されます。
応力を計算して、材料の強度から安全破壊率を割出し、書類を作成し検査法人検査科に提出します。
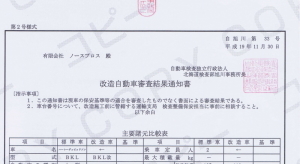
数週間の審査を経て、改造自動車審査結果通知書が降ります。この書類が降りれば、あとは車輌検査へ行くだけです。
いよいよ、改造車両を支局に検査に持ち込みます。
ライト・ブレーキなど保安基準に適合し、通常の車検の検査で寸法並びに重量を測定し、検査は終了です。
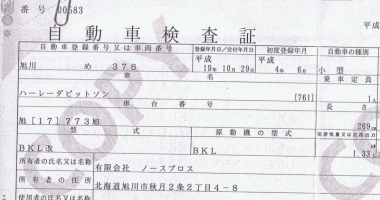
検査が合格したら、予て待ち望んだ公認車の誕生です!!
車名の変更はなく、型式に「改」が記載されます。これで、次回の車検から継続検査でOKとなります。